Cardiac Catheterization Lab Radiation Shielding Redesign
Outcome:
Designed and proposed a more efficient, convenient, and cost-effective radiation shield for use in a cardiac catheterization lab. I proposed a novel alternative material that prevents almost 100% of high energy ionizing radiation, compared to the current industry standard 60%. The sintering process in powder metallurgy is deemed the most efficient manufacturing method, in terms of quality and cost. With the team of two researchers and two doctors at Grady Hospital in Atlanta, a more convenient portable floor shield was also designed.
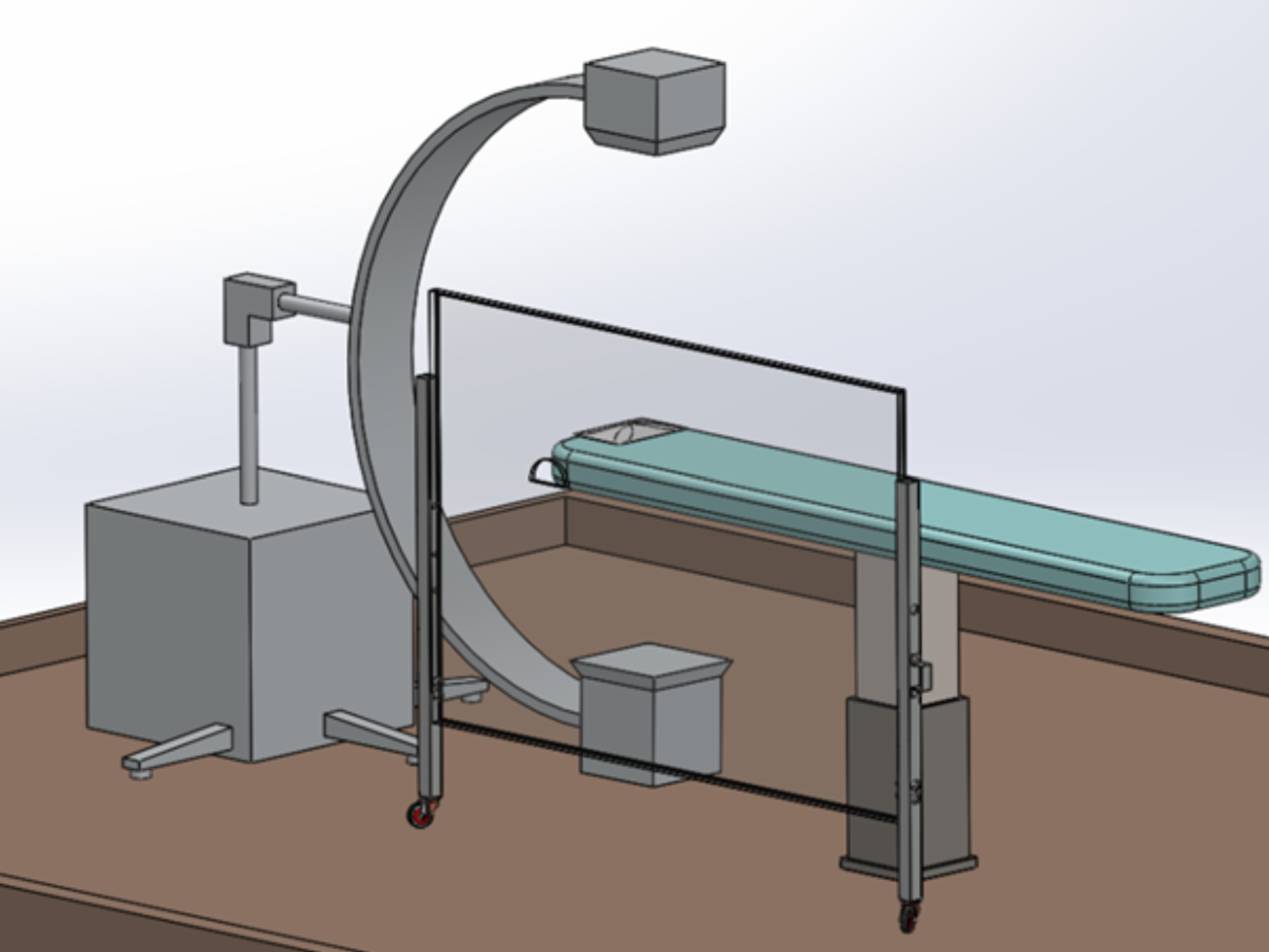
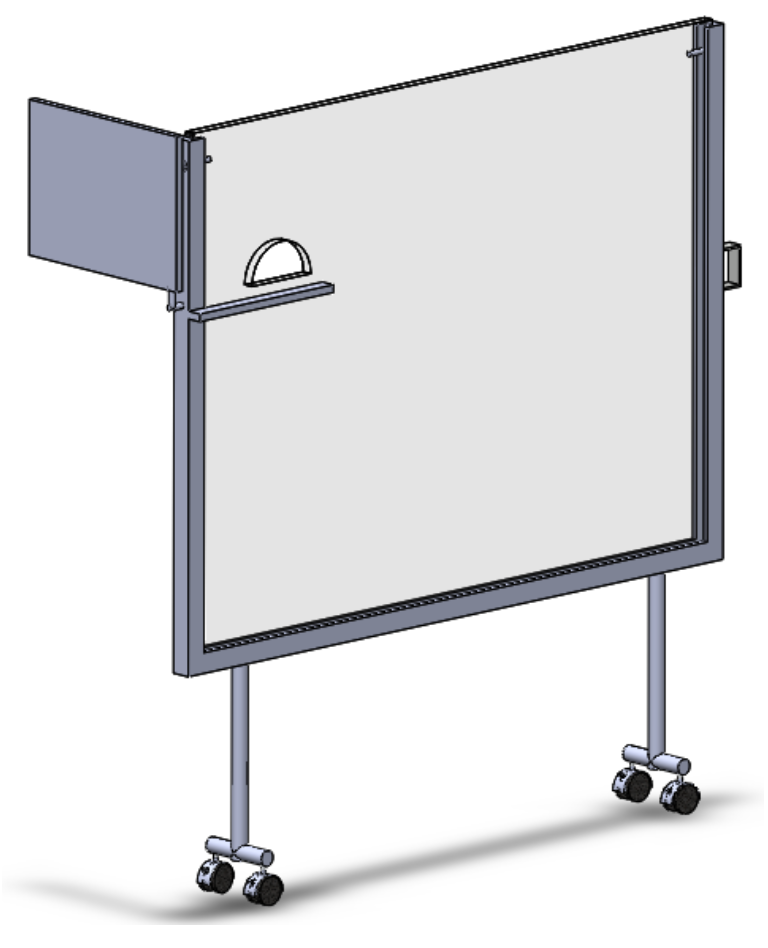
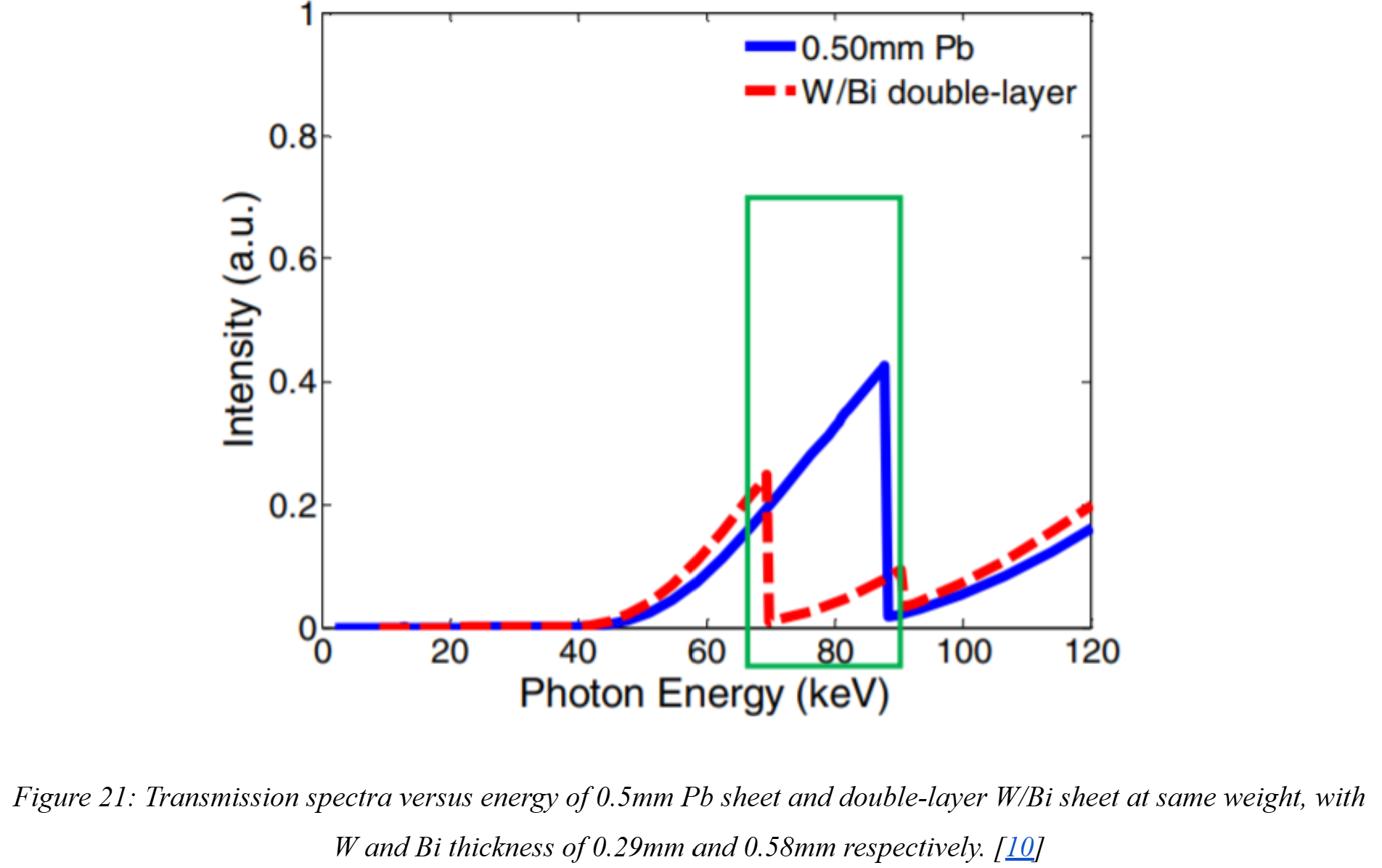
Motivation:
The most common ionizing radiation used in a cath-lab occurs in the X-ray field, typically with wavelengths in the range of 0.01 nm up to 10 nm. This corresponds to a photon energy range of 100 keV down to 100 eV. The well-documented dangers of such X-ray ionizing radiation arise from the radiation having enough energy to potentially damage DNA. These can lead to many health risks to exposed operators, including a small increase in likelihood of developing cancer in later life, and tissue effects (occurring at relatively high levels of radiation exposure) such as cataracts, skin reddening, and hair loss.
Radiation exposure in fluoroscopy equipment like C-arms comes from two main sources- “scatter” radiation that bounces off the patient's body and “leakage” radiation from the X-ray tube. Of the two sources of exposure, scatter radiation varies considerably more and is the higher contributor to overall exposure. With scatter radiation bouncing off the bed and patient, the most important body parts of the operator that need to be protected are the torso and head. The state-of-the-art shield used at Grady Hospital was quite small, inflexible and difficult to maneuver during procedures. Moreover, the leaded acrylic material was highly toxic and exhibited a blind absorption zone which allowed transmittance of high-energy radiation to operators.
Results:
Our client simply wanted us to choose a shield shape that maximized reflected radiation. However, I decided to change the foundation of the design completely by recommending a new radiation-absorbent metal alloy. To determine its effectiveness, I conversed with my professor and clients on a weekly basis, updating them on multiple papers I had read on the new material. I also carried out various simulations to predict its structural integrity and optical transparency. After months of meticulous research, we found that the final alloy reduced exposure by up to 40%, and our tests showed it had all the optical properties necessary to act as a transparent floor shield. From this experience, I learned the importance of challenging norms in order to create the best possible product, along with effectively communicating with a team to do so.
Project Report: